Eric Ayers
The trend of food manufacturers and retailers embracing trayless products using thermoformed packaging is one that’s steadily gaining steam and showing no signs of slowing down. According to Global Market Insights, a market research and consulting firm, the thermoform packaging market in North America was valued at more than $19 billion in 2023, up from $17.9 billion since 2021. The report cited the region’s “mature and well-established packaging industry, coupled with a high level of technological sophistication.” Not surprisingly, food and beverage is an industry that has discovered the numerous advantages that make thermoforming a go-to packaging option. Here are three advantages thermoform technology brings to packaging. What are your top reasons?
All-in-One Solution
One of the great advantages a thermoformer provides is packaging flexibility. For a customer that does custom cuts, custom meats, or made-to-order products, a thermoformer is the perfect solution. It can do vacuum skin packaging (VSP) and modified atmosphere packaging (MAP), run large variations of film types and thicknesses, and with the right combination of those features can almost double the shelf life of products such as red meat, poultry, fresh seafood, deli meats and many others.
Per unit, a thermoform packaged product is a bit more expensive than a traditional plastic bag, but the value that it provides from an appearance standpoint is that it is much more aesthetically pleasing for case ready or shelf presentation. This is a premium package that well represents the value of higher priced products. Thermoform packaging is also more durable, resulting in less product damage and less leakage. Finally, you can use a variety of recycled materials to boost your products’ green goals and initiatives.
Saddle Up
A subset of trayless packaging that is in high enough demand to be its own trend is saddlepacks. Derived from a package as if being folded over like a saddle on a horse’s back, saddlepacks are an increasingly common solution for bulk retail and commercial food operations involving breaking up large quantities of products into smaller individual packs that are then “saddled” together. Most often, the smaller packs within the full package are portioned and packaged by a scaling depositor to ensure equal weight in each pouch for ease of use.
Saddlepacks have found success in food operations largely due to their preservation qualities. When a 10-pound bag of chicken breasts is cut open, the timeline speeds up for every unit of that product to be used before it spoils. Having smaller packages allows users to open and use them as needed and let the film do its job of preserving the rest of the product’s shelf life. These saddled packs can also be separated for easier storage in fridges and freezers.
The Automation Factor
The main area of pushback I see from customers hesitant to embrace thermoform packaging is the cost. A retailer can use a 10-cent bag to package five pounds of meat, whereas it may cost up to 40 cents to package that same amount on a thermoformer. While that may not seem like a big difference, over the course of packaging a million pounds, 30 cents adds up to a big margin.
The answer to that dilemma is found in labor, or the lack thereof. Food manufacturers and retailers just don’t have the available staffing to manually pack bags anymore. The labor pool is not there to work in 40° weather, eight hours a day, six days a week. Using a thermoformer largely solves that issue by removing the manual process of hand packing products.
No matter what trends your customers are impacted by in 2024, having the right equipment is crucial to your operation. When you look to bring in new tray sealing, thermoforming, and wrapping equipment, be sure to speak with your sales representative about your needs both now and in the future.
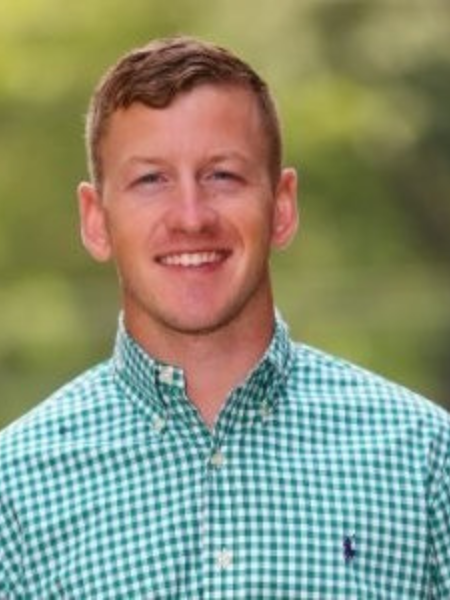
Subscribe to our email list for the latest in flexible packaging news.
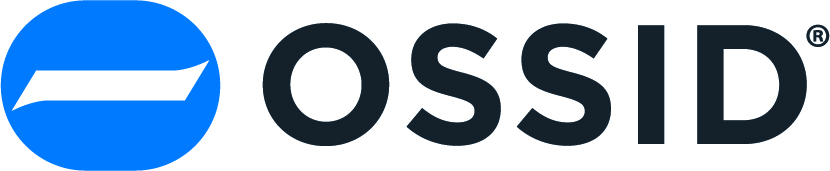
Ossid provides superior tray overwrapping, flow wrapping, weigh price labeling, case scales, and horizontal thermoform fill & seal machinery. We are committed to designing and building solutions that protect product quality and fully meet our customers’ production needs.