By Chris Shay
Good news, your food manufacturing company just landed a new contract that will more than double production of individually quick frozen (IQF) foods in the coming months. The bad news is, your current vertical form fill and seal machine may not be designed with the speed or sanitary attributes necessary to operate well in a cold, damp environment.
This is where the value of Matrix proves its worth.
Built for the cold
The biggest challenge of packaging IQF products is the environment itself. Most of these facilities are damp and kept below 32°. The bagger needs to be engineered to withstand the rigors of these demanding locales while still performing up to three shifts daily.
IQF applications are a specialty of Matrix. For more than 30 years Matrix has been building hygienic vertical form fill seal machines with a proven record of reliability and performance. The goal is designing a hygienic bagger to reduce contamination from forming in the first place by eliminating the harbor points where food particles and bacteria can collect. Matrix does this by using welded rounded frames with minimal fasteners in the food zones to reduce catch points and places for contamination to occur. Sloped roofs on electrical cabinets further act to eliminate water from pooling. Additionally, Matrix hygienic baggers are made with stainless steel instead of more porous aluminum, and can be fully washed down for regular cleanings. These are just some of the engineering designs that help make Matrix form fill and seal machines the right choice for IQF applications.
Beyond the bagger
While a new hygienic bagger can reach the required speeds, that alone may not provide you with the best possible solution. The aim of any IQF-focused packaging line is achieving the desired throughput. If the application calls for 150 bags per minute, Matrix can build that machine for you, no problem. But if the upstream processes cannot keep pace to adequately feeding the bagger, you’ll fall short of that targeted rate. It is critical to evaluate the entire line, both upstream and downstream of the bagger, to ensure each process is performing at a level to obtain the desired throughput.
A detailed evaluation of the line may identify additional areas where improvements can be made to maximize overall efficiency and production. This is where the power of ProMach makes a difference. Matrix is part of ProMach, a company with more than 50 product brands covering every function of the production line. If your project does outline other areas where ProMach brands can be beneficial, from labeling or coding, case forming, palletizing, stretch wrapping or anything in-between, ProMach delivers best-in-class product brands across the entire packaging spectrum. The true benefit to you is having one point of contact for your project from start to finish; you do not need to waste time and resources meeting and dealing with multiple vendors. This level of project management streamlines the planning process, installation, and start-up curve for packaging lines.
Anyone can sell you a bagger, but your best chances for long-term success is to partner with a reputable OEM that brings the expertise and industry know-how in the IQF space – and that partner is Matrix.
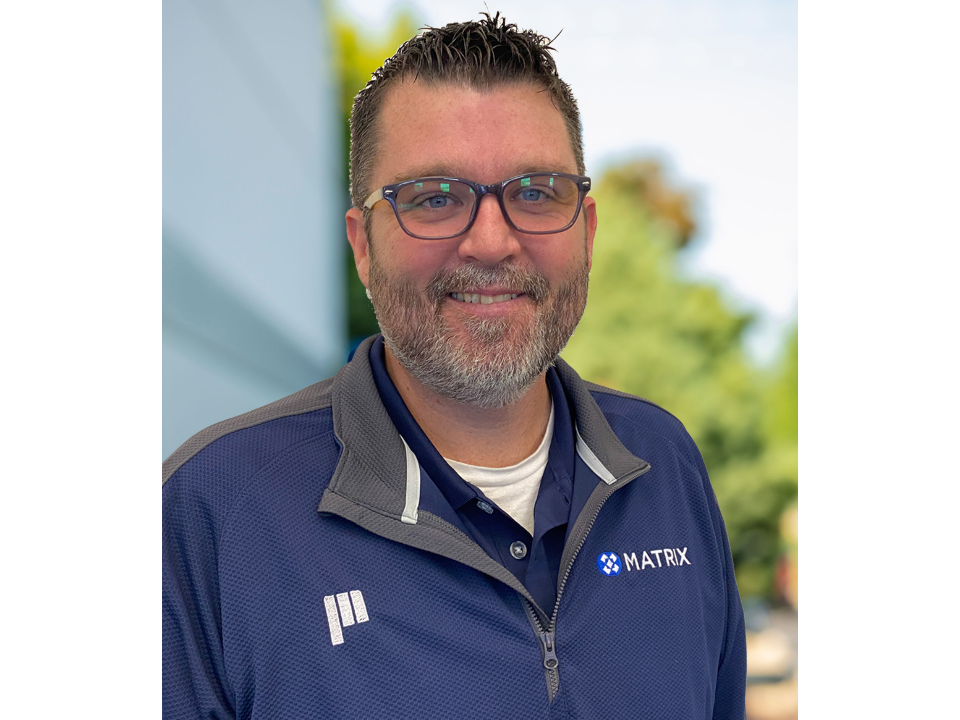
Subscribe to our email list for the latest in flexible packaging news.