Managing Innovation at Bartelt’s Film Compatibility Test Lab
Introducing Jeff Bakran, the Test Lab Manager at our film test lab here at Bartelt Packaging. With a focus on testing and evaluating pouches, Jeff ensures thorough assessment for both internal and customer-submitted samples.
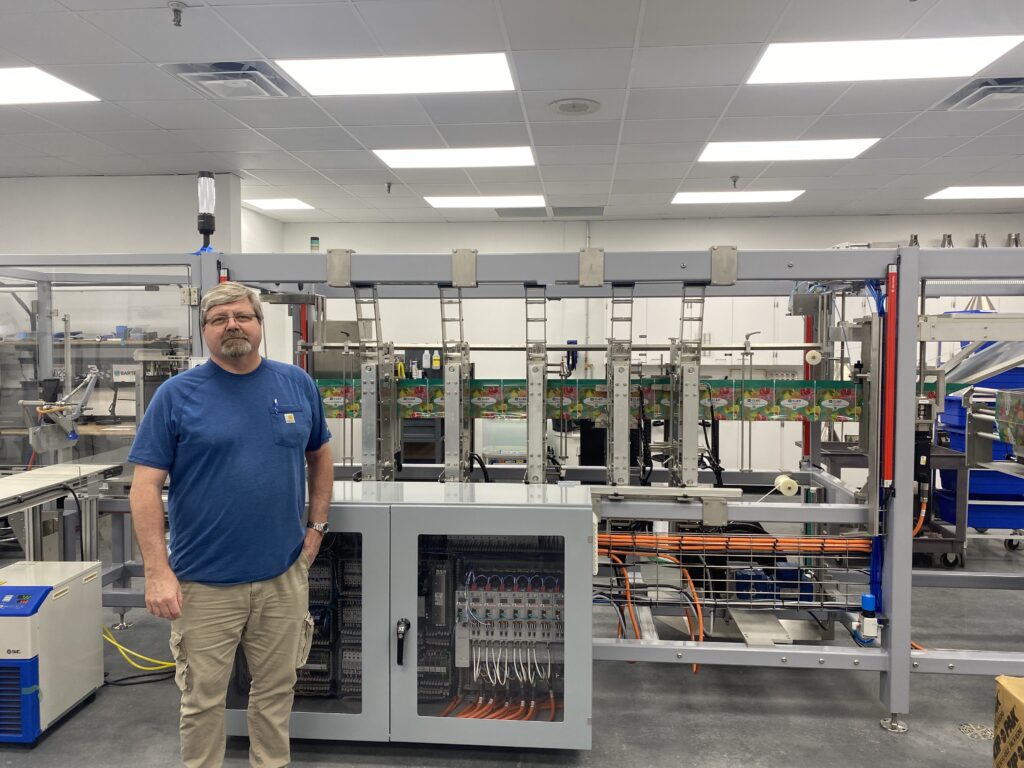
Understanding the Role: A Q&A with Jeff
Question: Can you tell us about your role as the test lab manager?
The core of my role is to test and evaluate film and zippers either internally or a customer submitted sample. It also includes assisting in the R&D lab with prototyping and proof-of-principle projects. Fill testing is also accomplished here, but we are still in the process of getting that equipment back on-line. The 3D print shop is in the Lab also, so I will print prototype parts and anything Engineering needs printed.
Goals and Objectives of the Film Compatibility Test Lab
Question: What are the primary objectives and goals of our film compatibility test lab?
The primary objective is the complete and accurate testing of any material that gets presented to the Lab. As far as goals are concerned, we would like to have a comprehensive database built up at some point in order to have a quick reference for similar materials that we test. Another goal is to have a well-defined understanding of how newer recyclable films react to the bag making process and stay on top of current film technology.
A Revamped Lab: Remodeling and Enhancements
Question: Could you please tell us about some of the improvements/remodeling that recently took place.
The Lab has recently gone through a COMPLETE overhaul, not only the space itself, but all the test equipment as well. A ground-up remodel was done on the Lab, New paint, ceiling, floor sealant, and cabinets. There was also a new window installed for complete visibility from the main building access, and new overhead door for equipment transfer in and out of the Lab.
The Key to Thorough and Reliable Testing
Question: How do you ensure that the film compatibility testing process is thorough and reliable?
All of our new test equipment was purchased calibrated and stays calibrated. We follow the same procedures for all the tests, which are recorded and saved in a common location.
Challenges and Materials: Navigating Film Compatibility
Question: What types of films are typically submitted to the test lab, and what are the most common compatibility challenges you encounter?
Lately, we have been getting a lot of recyclable and Recycle Ready films. These newer films are challenging in that the material does not handle heat well, and we will get stretching and burn through. The older, sturdier films do not present much of a problem because these have been ran on our equipment for years.
Cutting-Edge Equipment and Technology
Question: What specialized equipment and technologies do you use to conduct these tests?
New test equipment includes:
- TMI 32-76e Friction/Peel tester: This device allows us to do COF (coefficient of friction) tests and Peel tests.
- TMI TS-4 and TS-12 Heat Sealers: These new Heat Sealers allow us to manually construct pouches individually for various tests.
- SMZ745T-PS-HDS Digital Microscope System: We can inspect side seals and zipper seals up close, and it also has picture-taking capabilities to include in customer reports.
Driving Innovation: From Lab to Production
Question: How does the test lab contribute to the continuous improvement of our machines and packaging solutions?
Our engineering team has a platform to test different things on this machine. When we built this machine, we made sure to put enough room on it for future testing. This was designed not only to test film but for actual product testing.
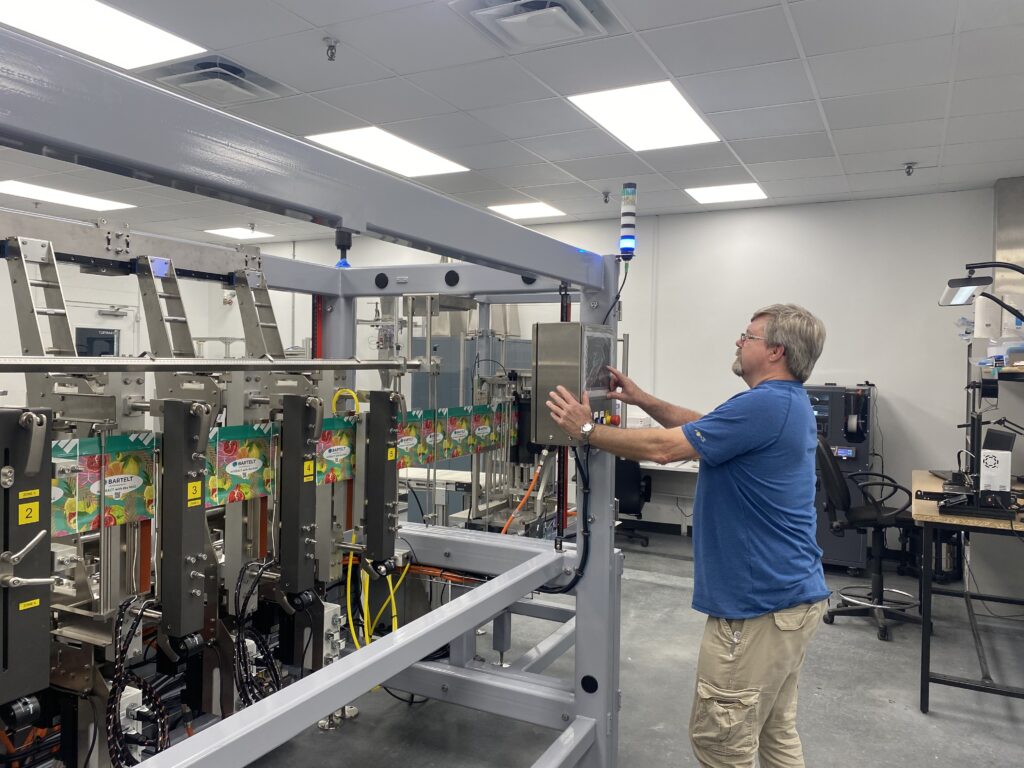
Staying Current with Industry Advancements
Question: How do you ensure that our film compatibility testing procedures are up to date with industry advancements and trends?
Our film compatibility testing procedures stay up to date with industry advancements and trends through a customer-driven approach. Our customers are highly responsive to consumer demands, so we closely monitor the preferences of end consumers. We also observed a shift from rigid packaging to flexible packaging, as they are easily transported and easy to use, making them more appealing to both customers and consumers.
Sustainability in Action
Question: How does our Film Compatibility Test Lab incorporate sustainability principles into its daily operations?
To ensure film compatibility, we follow a comprehensive step-by-step process in our lab. We begin by logging the testing information into our system and database. The first test involves measuring the film thickness using specialized equipment. Next, we assess the coefficient of friction, which requires a specific sample size. To create pouches for testing, we utilize a manual sealing station, adjusting the machine settings according to the customer’s specifications, including pouch size and zipper placement. The machine runs until we achieve a high-quality product that meets our standards for leak-proof performance.
Once we obtain what we believe to be a satisfactory result, we conduct a burst test by sealing the bag and subjecting it to a vacuum tank to assess its strength and resistance to breaking. Throughout the testing process, we maintain a report. This report is then submitted to the customers, providing them with insights into the film.
In conclusion, Bartelt Packaging’s Film Compatibility Test Lab, under the astute leadership of Jeff Bakran, stands as a testament to the company’s unwavering commitment to excellence. With cutting-edge equipment, rigorous testing protocols, and a customer-driven approach, the lab ensures that every film and pouch meets the highest standards of quality and performance. The recent overhaul and dedication to sustainability demonstrate Bartelt’s adaptability and forward-thinking mindset. As the packaging industry continues to evolve, this test lab remains at the forefront, driving innovation, and delivering solutions that not only meet but exceed the needs of its clients. With Bartelt’s Film Compatibility Test Lab, you can trust that your packaging materials are in the hands of experts dedicated to ensuring your success.
Subscribe to our email list for the latest in flexible packaging news.

Bartelt is a trusted manufacturer of pouching, cartoning, shrink wrapping, over wrapping, and case and tray packing systems, providing dependable and long-lasting solutions to food and non-food industries. Bartelt also operates as a master distributor for FLtècnics’ rollstock pouch machines. As the world’s first developer of intermittent motion horizontal form fill seal pouching machines, Bartelt is a true pioneer in automated packaging.