By Jared Rangel
Proper product packaging is an important ingredient in the recipe for a successful baking business. What that looks like has changed a bit over the years as the business model for bakeries has shifted from small, straight-to-shelf operations to companies with retailers nationwide. Customer demand has also changed to demand more inclusive options and more baked products overall. Only by understanding all these trends and how they can be accommodated in packaging machinery can a bakery find the perfect solution.
No Egg-ceptions: Hygienic Packaging
In the past, painted frame machines were a common choice, as wipe-down surfaces sufficiently met hygiene needs. Now, various longer shipping and shelf-life timelines have driven up the sanitation requirements for bakeries that supply any third-party retailers.
Allergens are another important consideration for bakery lines. The demand for gluten-free, nut-free, dairy-free and other safe alternative products for those with allergies has grown substantially. Any bakery producing these products understands that keeping the packaging equipment completely devoid of allergens is critical. Avoiding cross-contamination can be a matter of life and death, and the hygienic qualities of the packaging equipment cannot be anything less than perfection.
The package itself can also present a more sanitary environment for the baked goods, with options of modified atmosphere or air evacuation. In these scenarios, the air in the package is either removed completely or replaced with a different gas mixture. This creates an environment within the package that slows mold growth and preserves freshness.
In the Pie of the Beholder: Premade Vs. Pillow Bag
As with many business decisions, choosing the right package style is a balancing act. For baked goods, this is usually a sliding scale between aesthetics and capabilities.
Premade bags are a common first step for bakery businesses. These packages offer features such as 4-side seals and crisp, thick film with a specific look that accentuates the appeal of the item inside. However, opting for this packaging style limits the scale of production, as it is more time-consuming and requires packaging to be done by hand. Each bag is also more expensive and requires additional shipping and storage considerations, decreasing profit per unit.
Pillow pouches are the next step to help operations keep up with increased product demand. Instead of a premade bag, which is packed by hand, pillow pouches are made of roll stock and formed around the product on the line. They feature two end seals and a fin or longitudinal seal down the back for a completely automated solution. This option is more affordable and can be completed at a faster rate than premade bags. Bakeries can also run printed film with this method, which can help bridge the aesthetic gap between the two packaging styles.



The Cherry on Top: Machine Quality
Regardless of the type of bag, the machine packaging them needs to be high quality. Many operations have moved from a single shift of production to 24 hours because of the growth in demand for baked goods. Any machine stoppage or time-consuming maintenance impacts the company’s bottom line by the second. Buying a reliable machine may be a more expensive initial investment, but the difference in quality will quickly pay off the difference.
This confidence in the packaging machinery is particularly important in bakeries and other perishable product applications. Preparing food is a complex process, and several components need to come together to even get the product ready to be packaged. Having it all go to waste because food spoiled because the line was down or the packaging was faulty is completely unacceptable. Packaging equipment manufacturers need to do everything in their power to meet all the changing needs of the industry, make the machine easy to run and keep the operation as efficient as possible.
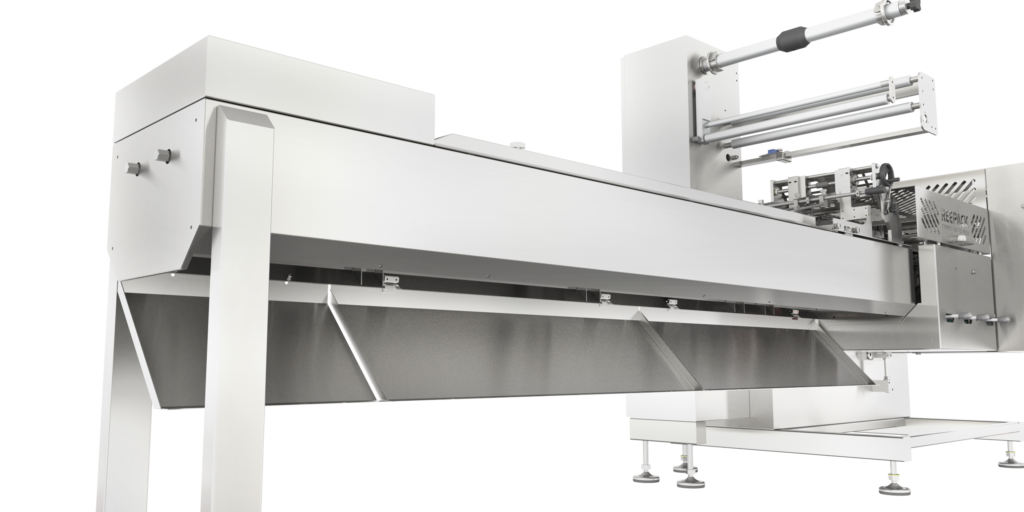
Subscribe to our email list for the latest in flexible packaging news.
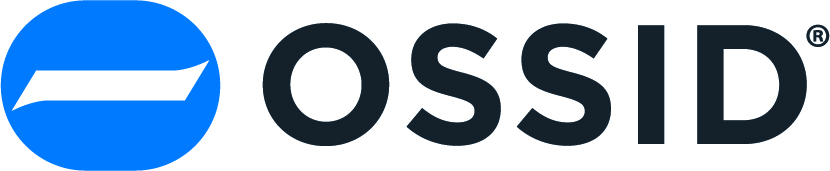
Ossid provides superior tray overwrapping, flow wrapping, weigh price labeling, case scales, and horizontal thermoform fill & seal machinery. We are committed to designing and building solutions that protect product quality and fully meet our customers’ production needs.