COLLABORATION AND COMPATIBLE MACHINERY PAVE THE WAY FOR SUSTAINABLE PACKAGING
By Troy Snader, Sr. Vice President of Business Development, ProMach’s Secondary Packaging Group
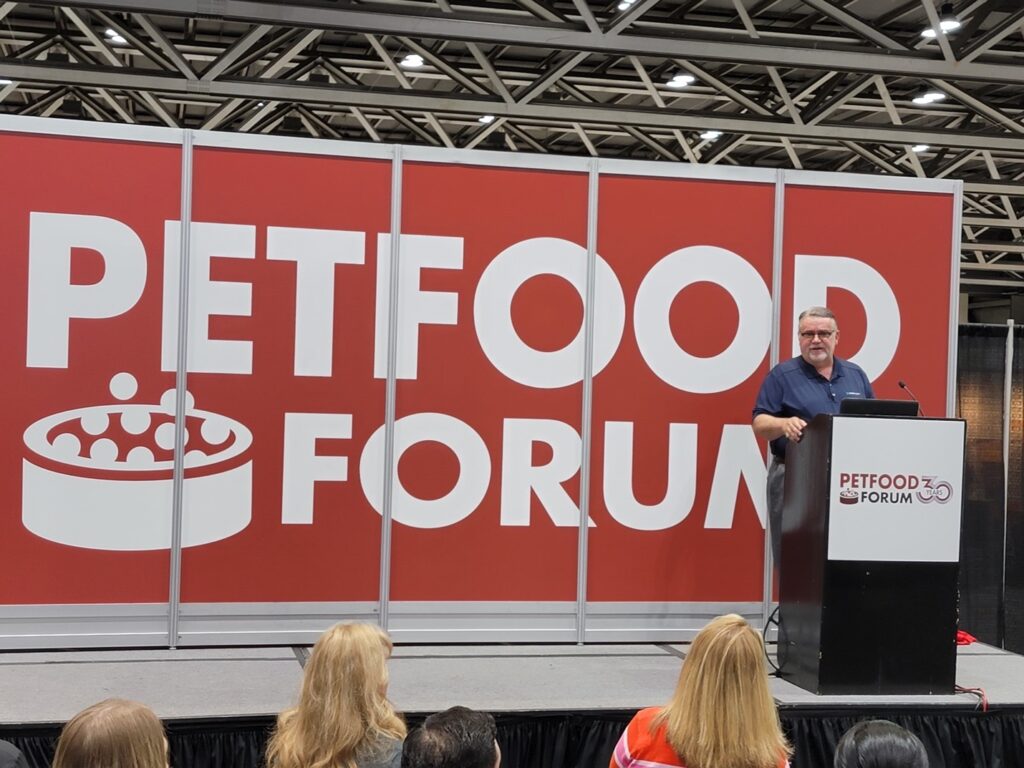
Walk through any pet store and you will see just how popular organic dog and cat food has become. According to petkeen.com, a staggering $22.8 billion was spent on organic pet food in 2020 – a figure that is expected to increase more than 10% by 2026.
As pet owners are embracing greener, healthier meals for their pets, they are also looking for a similar level of greenness in their food’s packaging. During a tech talk at the 2022 Petfood Forum, participants asked important questions about choices and options to improve the compatibility of form, fill and seal machinery with compostable and recyclable petfood packaging materials:
How would you characterize the state of petfood packaging today?
It is no surprise that consumers are behind the drive for sustainable petfood packaging. People today are looking for healthier, holistic options for their pets, and they are willing to pay more for petfood that contains better ingredients. While there are numerous green and holistic choices when it comes to petfood, there is a substantial push underway to extend green attributes to petfood packaging as well. The key in responding to these market needs is to provide the industry with machinery and packaging materials that meet the sustainability standards petfood manufacturers and consumers are looking for.
How are packaging OEMs responding to this call for sustainable petfood packaging?
Most of the recycled materials we use today are comprised of oriented polyethylene or polypropylene thermoplastic polymers. These two types of materials are mono layer, which are comprised of a single main material. In contrast, many common flexible packaging styles on the market today use laminated films, such as metallic or metalized films like aluminum. These differences in films have posed a challenge to packaging machines in the past, but most current designs in vertical and horizontal form fill seal machines are allowing pet food manufacturers to run these films using existing heat-sealing mechanisms, bars, cartridges, thermal couples, and other components.
What needs to be considered when running recycled or compostable materials?
While strong advances have been made, running recycled or compostable materials at high speeds on vertical and horizontal form fill seal machines can still be difficult, and remains a work in progress for some manufacturers. For example, oriented polyethylene has narrow (and lower) temperature sealing parameters compared to laminated film. What this means is that the optimal temperature window needed to create the seal on polyethylene film is limited, which slows production. By contrast, there is a 40-to-50-degree window to create the seals when running laminates – and a larger available window means faster production.
Why are stretch properties an important consideration for packaging films?
Recycled and compostable films also possess high stretch properties, and this is an important consideration if a customer is trying to run a registered bag. Typically, a registered bag has a 1-to-2-millimeter (plus or minus) cutoff. However, with these types of films, the customer is going to see a cutoff of 5-to-6 millimeters (plus or minus). That is a huge difference a lot of retailers won’t accept; frankly, that’s also out of range of what we would consider acceptable.
These are just a few of the factors that need to be considered and evaluated when running recycled or compostable films on packaging machinery. It is important for OEMs to work closely with material suppliers to innovate and develop practical solutions for more sustainable packaging.
What are some solutions for running green films on vertical form fill seal machinery?
We have developed several jaw-face styles that allow vertical form fill seal machines to seamlessly run a variety of film types, like green films. These machines are designed with a smooth HMI interface that allows for the operator to customize sealing for each film type. For example, the operator can dial in the specific heat temperature and length of sealing time, resulting in the perfect seal.
We also developed a pre-made pouch machine that employs several heating and cooling stations. This design innovation allows polyethylene and polypropylene films, which seal at a lower temperature, to be heated up slowly without burning and giving it a nice gradual heat transfer. This design also gives users more time on the machine to maintain their speed. In other words, instead of using one heat seal bar wrap, the machine uses two heat seal bars to maintain its speed integrity.
Why is cooling a factor that needs to be considered when running green films?
Mono-layer films tend to wrinkle on side edges or at the top seal. Adding cooling can help alleviate some of those seal wrinkles to the point where the petfood package is acceptable to retailers and their customers. Many packaging OEMs offer a cooling station which is important when running green films. Machines with integrated cooling stations can produce a largely wrinkle-free bag. Adding multiple heat stations, along with cooling are just two ways to help effectively run a variety of recycled and compostable films on vertical form fill seal machines.
What needs to be considered when purchasing petfood packaging machinery?
Green films in petfood packaging are constantly evolving. Market demands and customer buying preferences today may very well be different five years from now. The best way to stay ahead of those trends is having packaging machinery that is flexible to run a wide variety of films. It’s important to work with a reputable OEM. Reputable OEMs are paving the way forward for greener packaging by working closely with film suppliers to deliver the best practical solutions to petfood manufacturers and their customers.
About the Author
Troy Snader is the Senior Vice President of Business Development for ProMach’s Secondary Packaging Group. He can be contacted at Troy.Snader@ProMachBuilt.com. For more information about ProMach please visit www.ProMachBuilt.com.
Subscribe to our email list for the latest in flexible packaging news.
Plan to visit ProMach brand booths at the 2023 Petfood Forum May 1st – 3rd in Kansas City.

Matrix provides flexible packaging machinery solutions to customers worldwide. Vertical form, fill, seal; horizontal form, fill, seal; pre-made pouches; stickpacks and sachets, Matrix can help you find your flexible packaging solution.
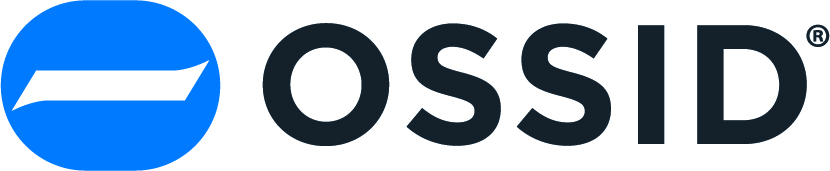
Ossid provides superior tray overwrapping, flow wrapping, weigh price labeling, case scales, and horizontal thermoform fill & seal machinery. We are committed to designing and building solutions that protect product quality and fully meet our customers’ production needs.